پیسنے والی ڈسک مختلف صنعتوں میں ایک اہم کردار ادا کرتی ہے، مواد کی تشکیل اور تکمیل میں سہولت فراہم کرتی ہے۔ تاہم، کسی دوسرے آلے کی طرح، وہ ان مسائل سے محفوظ نہیں ہیں جو ان کی کارکردگی اور کارکردگی کو متاثر کر سکتے ہیں۔ اس مضمون میں، ہم پیسنے والی ڈسک کے عام مسائل پر غور کریں گے، ان کی بنیادی وجوہات کو تلاش کریں گے، اور بغیر کسی رکاوٹ کے کام کے بہاؤ کے لیے موثر حل فراہم کریں گے۔
تعارف
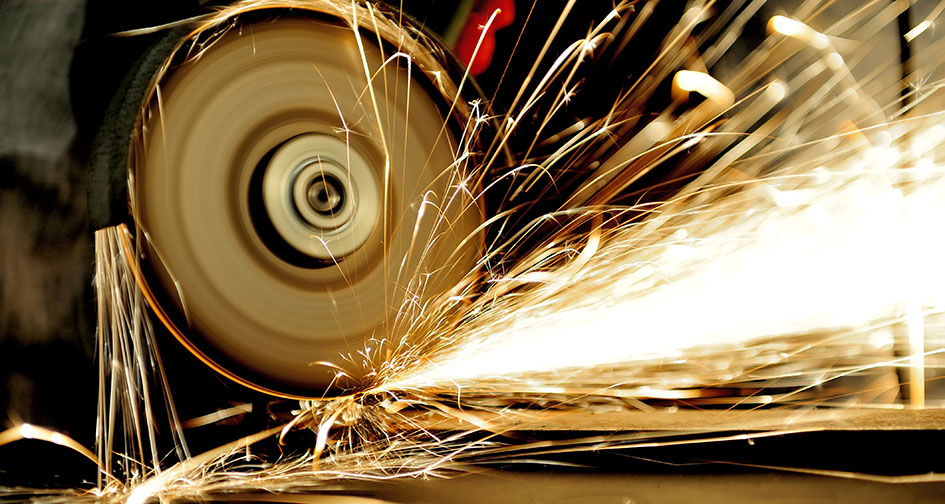
پیسنے والی ڈسکیں مختلف صنعتوں میں بنیادی کردار ادا کرتی ہیں، جو مواد کو ہٹانے، تشکیل دینے اور مکمل کرنے کے عمل کے لیے ضروری آلات کے طور پر کام کرتی ہیں۔ ان کی تعریف، صنعتوں میں اہمیت، اور درپیش عام مسائل کو سمجھنا ان کے استعمال کو بہتر بنانے اور موثر آپریشنز کو یقینی بنانے کے لیے بہت ضروری ہے۔
A. پیسنے والی ڈسکس کی تعریف
پیسنے والی ڈسکیں کھرچنے والے اوزار ہیں جو مشینی عمل میں مواد کی سطحوں کو کاٹنے، پیسنے یا پالش کرنے کے لیے استعمال ہوتے ہیں۔ یہ ڈسکس عام طور پر کھرچنے والے ذرات پر مشتمل ہوتے ہیں جو بیکنگ مواد سے جڑے ہوتے ہیں، ایک گھومنے والا ٹول بناتا ہے جو اضافی مواد، ہموار سطحوں، یا کناروں کو تیز کر سکتا ہے۔ وہ مختلف اشکال اور سائز میں آتے ہیں، ہر ایک کو مخصوص ایپلی کیشنز کے لیے ڈیزائن کیا گیا ہے۔
B. مختلف صنعتوں میں اہمیت
دھات کاری کی صنعت:
دھاتی ساخت اور مینوفیکچرنگ میں، پیسنے والی ڈسکیں دھاتی سطحوں کی تشکیل، ڈیبرنگ اور فنشنگ کے لیے اہم ہیں۔ وہ عام طور پر عین مطابق طول و عرض اور سطح کے معیار کو حاصل کرنے کے لیے زاویہ گرائنڈر کے ساتھ استعمال ہوتے ہیں۔
تعمیراتی صنعت:
تعمیراتی پیشہ ور کنکریٹ کی سطح کی تیاری، کھردری کناروں کو ہموار کرنے اور پتھر اور کنکریٹ جیسے مواد میں خامیوں کو دور کرنے جیسے کاموں کے لیے پیسنے والی ڈسک پر انحصار کرتے ہیں۔
آٹوموٹو انڈسٹری:
پیسنے والی ڈسکیں آٹوموٹیو سیکٹر میں ٹولز کو تیز کرنے سے لے کر دھاتی اجزاء کی تشکیل اور تکمیل تک کے کاموں کے لیے ضروری ہیں۔ وہ آٹوموٹو پرزوں کی درستگی اور معیار میں حصہ ڈالتے ہیں۔
لکڑی کے کام کی صنعت:
لکڑی کے کام کرنے والے لکڑی کی سطحوں کو شکل دینے اور ہموار کرنے کے لیے پیسنے والی ڈسک کا استعمال کرتے ہیں۔ یہ ڈسکس اضافی مواد کو ہٹانے، شکلوں کو بہتر بنانے اور مزید تکمیل کے لیے لکڑی کی تیاری میں موثر ہیں۔
جنرل مینوفیکچرنگ:
پیسنے والی ڈسکیں مینوفیکچرنگ کے مختلف عملوں میں ایپلی کیشنز تلاش کرتی ہیں جہاں عین مطابق مواد کو ہٹانے کی ضرورت ہوتی ہے، جس سے اعلیٰ معیار کے اجزاء کی پیداوار میں مدد ملتی ہے۔
C. عام مسائل کا سامنا
ڈسک پہننا اور کھرچنا:
مسلسل استعمال پیسنے والی ڈسک کے پہننے اور کھرچنے کا باعث بن سکتا ہے، جس سے اس کی کارکردگی متاثر ہوتی ہے۔ کارکردگی کو برقرار رکھنے کے لیے باقاعدہ معائنہ اور تبدیلی ضروری ہے۔
زیادہ گرم ہونا:
طویل استعمال کے دوران ضرورت سے زیادہ رگڑ زیادہ گرمی کا باعث بن سکتی ہے، جس سے ڈسک کی پائیداری اور تیار شدہ سطح کا معیار متاثر ہوتا ہے۔ ٹھنڈک کے مناسب اقدامات اور وقتاً فوقتاً وقفے ضروری ہیں۔
جمنا:
پیسنے والی ڈسکیں مواد کی باقیات کو جمع کر سکتی ہیں، ان کی تاثیر کو کم کرتی ہیں۔ باقاعدگی سے صفائی یا اینٹی کلاگنگ خصوصیات کے ساتھ ڈسکس کا انتخاب اس مسئلے کو روکنے میں مدد کرتا ہے۔
کمپن اور ہلچل:
عدم توازن یا غیر مساوی لباس کے نتیجے میں کمپن یا ڈوبنے کا سبب بن سکتا ہے، جس سے تکمیل کے معیار اور آپریشن کی حفاظت دونوں متاثر ہوتی ہیں۔ مناسب تنصیب اور توازن اہم ہے۔
ڈسک کا غلط انتخاب:
کسی مخصوص مواد یا ایپلی کیشن کے لیے غلط قسم کی پیسنے والی ڈسک کا انتخاب ناکارہ ہونے اور ممکنہ نقصان کا باعث بن سکتا ہے۔ مادی مطابقت کی بنیاد پر مناسب انتخاب ضروری ہے۔
ان ٹولز پر انحصار کرنے والی صنعتوں کے لیے پیسنے والی ڈسکس سے وابستہ تعریف، اہمیت اور ممکنہ چیلنجز کو سمجھنا ضروری ہے۔ عام مسائل کو حل کرنے اور مناسب استعمال کو یقینی بنا کر، صنعتیں اپنی متعلقہ ایپلی کیشنز میں پیسنے والی ڈسک کی تاثیر کو زیادہ سے زیادہ کر سکتی ہیں۔
پیسنے والی ڈسکس پر پہننا اور آنسو
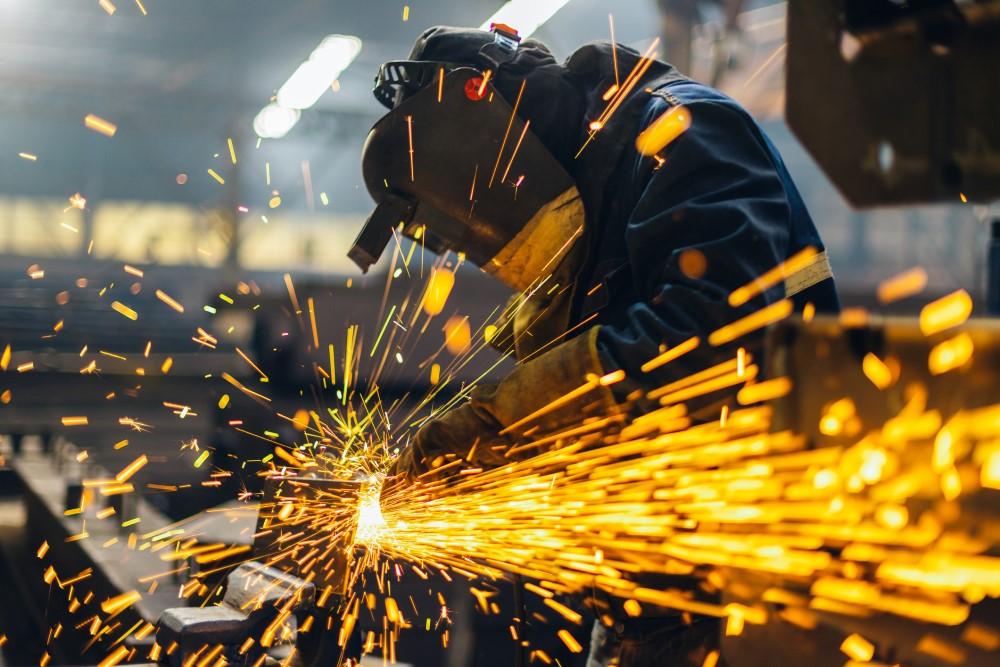
پیسنے والی ڈسکس مختلف صنعتوں میں ضروری ٹولز ہیں، جو دھاتی تانے بانے سے لے کر کنکریٹ پالش کرنے تک کے کاموں کے لیے ضروری رگڑ فراہم کرتے ہیں۔ پیسنے والی ڈسکس پر ٹوٹ پھوٹ میں کردار ادا کرنے والے عوامل کو سمجھنا ان کی کارکردگی کو بہتر بنانے اور حفاظت کو یقینی بنانے کے لیے بہت ضروری ہے۔
مواد کی سختی اور ساخت:
سختی کی تبدیلی:پیسنے والی ڈسکس مختلف سختی کی سطحوں کے ساتھ مواد کا سامنا کرتی ہے۔ دھات اور کنکریٹ جیسے کھرچنے والے مواد سختی میں نمایاں طور پر مختلف ہو سکتے ہیں۔ سخت مواد کے خلاف مسلسل پیسنا پہننے کو تیز کرتا ہے۔
مواد کی ساخت:گراؤنڈ ہونے والے مواد میں کھرچنے والے عناصر کی موجودگی پیسنے والی ڈسک پر پہننے کو متاثر کر سکتی ہے۔ کھرچنے والے ذرات ڈسک کے نیچے پہننے کو تیز کر سکتے ہیں۔
پیسنے کا دباؤ اور قوت:
ضرورت سے زیادہ دباؤ:پیسنے والی ڈسک پر ضرورت سے زیادہ دباؤ ڈالنا جلدی پہننے کا باعث بن سکتا ہے۔ ڈسک پر غیر ضروری دباؤ سے بچنے کے لیے مخصوص ایپلیکیشن کے لیے تجویز کردہ دباؤ کا استعمال کرنا ضروری ہے۔
ناکافی قوت: دوسری طرف، ناکافی قوت کے نتیجے میں لمبے عرصے تک پیسنا، اضافی رگڑ اور گرمی پیدا ہو سکتی ہے، جو پہننے میں حصہ ڈال سکتی ہے۔
ڈسک کوالٹی اور کمپوزیشن:
کھرچنے والے مواد کا معیار:پیسنے والی ڈسک میں استعمال ہونے والے کھرچنے والے مواد کا معیار اس کی عمر کو نمایاں طور پر متاثر کرتا ہے۔ اعلی معیار کے کھرچنے والے مواد پہننے کے خلاف مزاحمت کرتے ہیں اور نفاست کو زیادہ دیر تک برقرار رکھتے ہیں۔
بانڈنگ ایجنٹ:بانڈنگ ایجنٹ جو کھرچنے والے ذرات کو ایک ساتھ رکھتا ہے ایک اہم کردار ادا کرتا ہے۔ ایک اچھی طرح سے ڈیزائن کردہ بانڈنگ ایجنٹ ڈسک کی پائیداری کو بڑھاتا ہے۔
کام کے ماحول کے حالات:
درجہ حرارت:پیسنے کے دوران پیدا ہونے والا بلند درجہ حرارت ڈسک کی ساخت کو متاثر کر سکتا ہے۔ ضرورت سے زیادہ گرمی بانڈنگ ایجنٹ کو کمزور کرتی ہے اور لباس کو تیز کرتی ہے۔
نمی اور آلودگی:کام کے ماحول میں نمی یا آلودگیوں کی نمائش پیسنے والی ڈسک کی سالمیت کو متاثر کر سکتی ہے، جس کی وجہ سے تیزی سے پہننا پڑتا ہے۔
آپریٹر تکنیک:
مناسب تکنیک:آپریٹر کی مہارت اور تکنیک اہم ہیں۔ غلط استعمال، جیسے غلط زاویوں پر پیسنا یا ضرورت سے زیادہ طاقت کا استعمال، ناہموار لباس میں حصہ ڈال سکتا ہے اور ڈسک کی لمبی عمر کو کم کر سکتا ہے۔
باقاعدہ معائنہ:آپریٹرز کو چاہیے کہ وہ باقاعدگی سے گرائنڈنگ ڈسک کا معائنہ کریں تاکہ کسی بھی نقصان یا پہننے کی علامت ہو۔ ایک خاص نقطہ سے باہر پہننے والی ڈسکس کو فوری طور پر تبدیل کیا جانا چاہئے۔
ڈسک سائز اور RPM مطابقت:
درست سائز:چکی کے لیے صحیح ڈسک کا سائز استعمال کرنا بہت ضروری ہے۔ غلط سائز کی ڈسکیں غیر مساوی طور پر پہن سکتی ہیں یا حفاظتی خطرات لاحق ہو سکتی ہیں۔
RPM مطابقت:پیسنے والی ڈسک کے لیے تجویز کردہ انقلابات فی منٹ (RPM) پر عمل کرنا بہترین کارکردگی کو یقینی بناتا ہے اور قبل از وقت پہننے سے روکتا ہے۔
باقاعدگی سے دیکھ بھال، تجویز کردہ آپریٹنگ حالات کی پابندی، اور کام کے لیے صحیح پیسنے والی ڈسک کا انتخاب ٹوٹ پھوٹ کو کم کرنے کے لیے ضروری مشقیں ہیں۔ پہننے پر اثر انداز ہونے والے عوامل کو سمجھ کر، آپریٹرز پیسنے والی ڈسک کی لمبی عمر اور کارکردگی کو بڑھا سکتے ہیں، پیسنے کے محفوظ اور زیادہ پیداواری آپریشنز میں حصہ ڈال سکتے ہیں۔
ناہموار پیسنا
ناہموار پیسنے سے مراد ایسی صورت حال ہے جہاں سطح زمینی ہونے کی وجہ سے مستقل اور ہموار تکمیل حاصل نہیں ہوتی ہے۔ یہ مسئلہ مختلف وجوہات کی بناء پر پیدا ہوسکتا ہے اور ورک پیس کے معیار کو متاثر کرسکتا ہے۔ یہاں عام عوامل ہیں جو ناہموار پیسنے اور ممکنہ حل میں حصہ ڈالتے ہیں:
پیسنے والے پہیے کا غلط انتخاب:
حل:اس بات کو یقینی بنائیں کہ پیسنے والا پہیہ مٹی کے لیے موزوں ہے۔ مختلف مواد کو مخصوص کھرچنے والی خصوصیات کی ضرورت ہوتی ہے۔ درخواست کے لیے صحیح پہیے کی قسم، گرٹ سائز، اور بانڈ کا انتخاب کریں۔
غلط پہیے کی ڈریسنگ:
وجہ:ایک پیسنے والا پہیہ جو مناسب طریقے سے نہیں پہنا جاتا ہے ناہموار لباس اور غیر موثر کاٹنے کا باعث بن سکتا ہے۔
حل:پیسنے والے پہیے کو اس کی شکل کو برقرار رکھنے اور کسی بھی جمع شدہ ملبے کو ہٹانے کے لیے باقاعدگی سے کپڑے پہنیں۔ مناسب ڈریسنگ مسلسل کاٹنے کی سطح کو یقینی بناتی ہے۔
ناکافی پیسنے والا سیال یا کولنٹ:
وجہ:پیسنے والے سیال کے ناکافی یا غلط استعمال کے نتیجے میں رگڑ اور گرمی میں اضافہ ہو سکتا ہے، جس کے نتیجے میں ناہموار پیسنا ہو سکتا ہے۔
حل:گرمی کو ختم کرنے اور رگڑ کو کم کرنے کے لیے مناسب پیسنے والے سیال یا کولنٹ کا استعمال کریں۔ یکساں نتائج حاصل کرنے کے لیے مناسب ٹھنڈک ضروری ہے۔
غلط پیسنے کے پیرامیٹرز:
وجہ:پیسنے کے غلط پیرامیٹرز جیسے کہ ضرورت سے زیادہ رفتار، فیڈ ریٹ، یا کٹ کی گہرائی کا استعمال ناہموار پیسنے کا باعث بن سکتا ہے۔
حل:مواد اور درخواست کی ضروریات کے مطابق پیسنے کے پیرامیٹرز کو ایڈجسٹ کریں۔ بہترین ترتیبات کے لیے مینوفیکچررز کی سفارشات کا حوالہ دیں۔
پہنا ہوا پیسنے والا وہیل:
وجہ:ایک بوسیدہ پیسنے والا پہیہ ایک مستقل کٹنگ سطح فراہم نہیں کر سکتا، جس کے نتیجے میں ناہموار پیسنا ہوتا ہے۔
حل:پیسنے والے پہیے کو تبدیل کریں جب یہ اپنی قابل استعمال زندگی کے اختتام پر پہنچ جائے۔ پہننے کی علامات کے لیے پہیے کا باقاعدگی سے معائنہ کریں۔
غیر مساوی دباؤ یا فیڈ کی شرح:
وجہ:پیسنے کے دوران غیر مساوی دباؤ یا متضاد فیڈ کی شرحیں فاسد مواد کو ہٹانے کا باعث بن سکتی ہیں۔
حل:یکساں دباؤ لگائیں اور پورے ورک پیس میں فیڈ کی مستقل شرح برقرار رکھیں۔ آپریٹر کی مہارت اور تفصیل پر توجہ اہم ہے۔
مشین کے مسائل:
وجہ:پیسنے والی مشین کے ساتھ مکینیکل مسائل، جیسے غلط ترتیب یا تکلے کے مسائل، ناہموار پیسنے کا نتیجہ ہو سکتے ہیں۔
حل:پیسنے والی مشین پر باقاعدگی سے دیکھ بھال کی جانچ کریں۔ مناسب فعالیت کو یقینی بنانے کے لیے کسی بھی مکینیکل مسائل کو فوری طور پر حل کریں۔
ورک پیس فکسچرنگ:
وجہ:ناقص طور پر محفوظ یا غلط طریقے سے منسلک ورک پیس ناہموار پیسنے کا باعث بن سکتے ہیں۔
حل:ورک پیس کی مناسب فکسچرنگ اور سیدھ کو یقینی بنائیں۔ پیسنے کے عمل کے دوران نقل و حرکت کو روکنے کے لیے اسے مضبوطی سے محفوظ کریں۔
ناہموار پیسنے کو حل کرنے کے لیے مناسب سازوسامان کے سیٹ اپ، درست آپریٹنگ پیرامیٹرز، اور دیکھ بھال کے باقاعدہ طریقوں کے امتزاج کی ضرورت ہوتی ہے۔ آپریٹرز کو پیسنے والی ایپلی کیشنز میں اعلیٰ معیار اور مستقل نتائج حاصل کرنے کے لیے فوری طور پر مسائل کی نشاندہی کرنے اور ان کو درست کرنے کی تربیت دی جانی چاہیے۔ باقاعدگی سے معائنہ اور بہترین طریقوں کی پابندی پیسنے کے عمل کے دوران موثر اور یکساں مواد کو ہٹانے میں معاون ہے۔
زیادہ گرمی کے مسائل
پیسنے کے دوران زیادہ گرم ہونا ایک عام مسئلہ ہے جو پیسنے والے پہیے اور ورک پیس دونوں کی کارکردگی کو متاثر کر سکتا ہے۔ ضرورت سے زیادہ گرمی مختلف مسائل کا باعث بن سکتی ہے، بشمول پہیے کی زندگی میں کمی، ورک پیس کو تھرمل نقصان، اور مجموعی طور پر پیسنے کی کارکردگی میں کمی۔ زیادہ گرمی کے مسائل سے نمٹنے کے لیے ممکنہ وجوہات اور حل یہ ہیں:
غلط پیسنے کے پیرامیٹرز:
وجہ:پیسنے کے غلط پیرامیٹرز کا استعمال، جیسے ضرورت سے زیادہ رفتار، فیڈ ریٹ، یا کٹ کی گہرائی، اضافی گرمی پیدا کر سکتی ہے۔
حل:پیسنے کے پیرامیٹرز کو تجویز کردہ حد کے اندر ایڈجسٹ کریں۔ زمینی مواد کی بنیاد پر بہترین ترتیبات کے لیے مینوفیکچرر کے رہنما خطوط سے مشورہ کریں۔
ناکافی ٹھنڈک یا چکنا:
وجہ:کولنٹ یا پیسنے والے سیال کے ناکافی استعمال کے نتیجے میں رگڑ اور گرمی بڑھ سکتی ہے۔
حل:پیسنے کے عمل کے دوران کولنٹ یا چکنا کرنے والے کی مناسب فراہمی کو یقینی بنائیں۔ مناسب ٹھنڈک گرمی کو ختم کرنے میں مدد کرتا ہے اور تھرمل نقصان کو روکتا ہے۔
وہیل کا غلط انتخاب:
وجہ:مٹیریل گراؤنڈ ہونے کے لیے نامناسب تصریحات کے ساتھ پیسنے والے پہیے کا انتخاب زیادہ گرمی کا باعث بن سکتا ہے۔
حل:مخصوص ایپلی کیشن کے لیے صحیح کھرچنے والی قسم، گرٹ سائز، اور بانڈ کے ساتھ پیسنے والا وہیل منتخب کریں۔ پہیے کو مواد سے ملانا گرمی کی پیداوار کو کم کرتا ہے۔
ورک پیس مواد کے مسائل:
وجہ:کچھ مواد، خاص طور پر جن میں تھرمل چالکتا کم ہوتی ہے، پیسنے کے دوران زیادہ گرم ہونے کا زیادہ خطرہ ہوتا ہے۔
حل:کم تھرمل چالکتا والے مواد کے لیے پیسنے کے پیرامیٹرز کو ایڈجسٹ کریں۔ گرمی سے متعلق حساس مواد کے لیے ڈیزائن کردہ خصوصی پیسنے والے پہیے کے استعمال پر غور کریں۔
وہیل ڈریسنگ کے مسائل:
وجہ:پیسنے والے پہیے کی بے ضابطگی یا غلط ڈریسنگ ناہموار رابطے اور گرمی کی تعمیر کا باعث بن سکتی ہے۔
حل:پیسنے والے پہیے کو اس کی شکل کو برقرار رکھنے اور کسی بھی گلیزنگ یا جمع شدہ ملبے کو ہٹانے کے لیے اسے باقاعدگی سے تیار کریں۔ مناسب طریقے سے ملبوس پہیے مسلسل پیسنے کی کارکردگی کو یقینی بناتے ہیں۔
مشین کی ناکافی دیکھ بھال:
وجہ:پیسنے کی ناقص دیکھ بھال کرنے والی مشینیں زیادہ گرمی کے مسائل میں حصہ ڈال سکتی ہیں۔
حل:پیسنے والی مشین پر باقاعدگی سے دیکھ بھال کریں، بشمول کولنٹ سسٹم کی جانچ کرنا، وہیل ڈریسنگ کے سامان کا معائنہ کرنا، اور مناسب سیدھ کو یقینی بنانا۔ کسی بھی مکینیکل مسائل کو فوری طور پر حل کریں۔
ناکافی وہیل کولنٹ کا بہاؤ:
وجہ:پیسنے والے زون میں کولنٹ کا ناکافی بہاؤ گرمی کی کھپت میں کمی کا باعث بن سکتا ہے۔
حل:کولنٹ کی ترسیل کے نظام کو چیک کریں اور اسے بہتر بنائیں۔ اس بات کو یقینی بنائیں کہ ٹھنڈک کی کارکردگی کو برقرار رکھنے کے لیے کولنٹ مؤثر طریقے سے گرائنڈنگ زون تک پہنچے۔
ضرورت سے زیادہ پیسنے کا وقت:
وجہ:بغیر وقفے کے طویل پیسنے کے سیشن گرمی کے اضافے میں معاون ثابت ہو سکتے ہیں۔
حل:وقفے وقفے سے پیسنے کو لاگو کریں اور ضرورت سے زیادہ گرمی کو جمع ہونے سے روکنے کے لیے وقفے کی اجازت دیں۔ یہ نقطہ نظر بڑے یا مشکل پیسنے والے کاموں کے لیے خاص طور پر اہم ہے۔
پیسنے میں زیادہ گرمی کے مسائل کو حل کرنے کے لیے ایک جامع نقطہ نظر کی ضرورت ہوتی ہے جس میں سازوسامان کا مناسب سیٹ اپ، مناسب پیسنے کے پیرامیٹرز، اور دیکھ بھال کے باقاعدہ طریقے شامل ہوں۔ آپریٹرز کو پیسنے کے عمل کے دوران گرمی کی پیداوار کی نگرانی اور کنٹرول کرنا چاہیے تاکہ بہترین کارکردگی، آلے کی توسیعی زندگی، اور اعلیٰ معیار کے نتائج کو یقینی بنایا جا سکے۔
کمپن کے خدشات
پیسنے کی کارروائیوں کے دوران ضرورت سے زیادہ کمپن مختلف مسائل کا باعث بن سکتی ہے، بشمول سطح کی کوالٹی میں کمی، ٹول پہننے میں اضافہ، اور پیسنے والی مشین کو ممکنہ نقصان۔ درست اور موثر پیسنے کے عمل کو حاصل کرنے کے لیے کمپن کے خدشات کو دور کرنا بہت ضروری ہے۔ کمپن کے مسائل کو کم کرنے کی ممکنہ وجوہات اور حل یہ ہیں:
ناہموار پہیے کا لباس:
وجہ:پیسنے والے پہیے پر فاسد لباس کے نتیجے میں ورک پیس کے ساتھ ناہموار رابطہ ہوسکتا ہے، جس سے کمپن ہوتی ہے۔
حل:مسلسل اور ہموار سطح کو برقرار رکھنے کے لیے پیسنے والے پہیے کا باقاعدگی سے معائنہ کریں اور کپڑے پہنیں۔ پہیے کی مناسب دیکھ بھال کمپن کو کم کرنے میں مدد کرتی ہے۔
غیر متوازن پیسنے والا پہیہ:
وجہ:پیسنے والے پہیے میں عدم توازن، چاہے ناہموار لباس یا مینوفیکچرنگ نقائص کی وجہ سے، کمپن کا باعث بن سکتا ہے۔
حل:وہیل بیلنسر کا استعمال کرتے ہوئے پیسنے والے پہیے کو بیلنس کریں۔ توازن وزن کی تقسیم کو یقینی بناتا ہے اور آپریشن کے دوران کمپن کو کم کرتا ہے۔
ناکافی مشین کیلیبریشن:
وجہ:مشین کے اجزاء کی ناقص انشانکن یا غلط ترتیب، جیسے وہیل اسپنڈل یا ورک ٹیبل، کمپن میں حصہ ڈال سکتے ہیں۔
حل:مناسب فعالیت کو یقینی بنانے کے لیے مشین کے اجزاء کو باقاعدگی سے کیلیبریٹ اور سیدھ میں رکھیں۔ مشین سیٹ اپ اور سیدھ میں لانے کے لیے مینوفیکچرر کی ہدایات پر عمل کریں۔
ورک پیس کا عدم توازن:
وجہ:ایک ناہموار یا غلط طریقے سے محفوظ شدہ ورک پیس عدم توازن پیدا کر سکتا ہے اور کمپن پیدا کر سکتا ہے۔
حل:ورک پیس کو مناسب طریقے سے محفوظ کریں، اس بات کو یقینی بناتے ہوئے کہ یہ یکساں طور پر پوزیشن میں ہے اور کلیمپڈ ہے۔ پیسنے کے عمل کو شروع کرنے سے پہلے عدم توازن کے مسائل کو حل کریں۔
وہیل کا غلط انتخاب:
وجہ:نامناسب تصریحات کے ساتھ پیسنے والے پہیے کا استعمال کمپن کا باعث بن سکتا ہے۔
حل:پیسنے والی وہیل کا انتخاب کریں جس میں مٹیریل گراؤنڈ ہونے کے لیے صحیح کھرچنے والی قسم، گرٹ سائز اور بانڈ ہو۔ پہیے کو ایپلی کیشن سے ملانا کمپن کو کم کرتا ہے۔
مشین کا پہننا اور آنسو:
وجہ:ٹوٹے ہوئے یا خراب شدہ مشین کے اجزاء، جیسے بیرنگ یا اسپنڈلز، کمپن میں حصہ ڈال سکتے ہیں۔
حل:پہنے ہوئے مشین کے پرزوں کا باقاعدگی سے معائنہ کریں اور تبدیل کریں۔ مناسب دیکھ بھال ضرورت سے زیادہ کمپن کو روکنے میں مدد کرتی ہے اور پیسنے والی مشین کی زندگی کو بڑھاتی ہے۔
کولنٹ کا ناکافی بہاؤ:
وجہ:پیسنے والے زون میں کولنٹ کا ناکافی بہاؤ گرمی کی تعمیر اور کمپن کا نتیجہ بن سکتا ہے۔
حل:مناسب ٹھنڈک کو یقینی بنانے کے لیے کولنٹ کی ترسیل کے نظام کو بہتر بنائیں۔ مؤثر ٹھنڈک تھرمل توسیع اور سکڑاؤ کے خطرے کو کم کرتی ہے، جو کمپن کا باعث بن سکتی ہے۔
ٹول ہولڈر کے مسائل:
وجہ:ٹول ہولڈر یا اسپنڈل انٹرفیس کے ساتھ مسائل کمپن متعارف کروا سکتے ہیں۔
حل:اس بات کو یقینی بنائیں کہ ٹول ہولڈر محفوظ طریقے سے نصب ہے اور سپنڈل کے ساتھ مناسب طریقے سے منسلک ہے۔ کمپن کو کم سے کم کرنے کے لیے اعلیٰ معیار کے اور مناسب طریقے سے دیکھ بھال کرنے والے ٹول ہولڈرز کا استعمال کریں۔
مشین فاؤنڈیشن:
وجہ:ناقص مشین فاؤنڈیشن یا ناکافی مدد کمپن کو بڑھا سکتی ہے۔
حل:یقینی بنائیں کہ پیسنے والی مشین ایک مستحکم اور مناسب طریقے سے ڈیزائن کی گئی بنیاد پر نصب ہے۔ مشین میں منتقل ہونے والی کمپن کو کم سے کم کرنے کے لیے ساختی مسائل کو حل کریں۔
پیسنے میں کمپن کے خدشات کو مؤثر طریقے سے حل کرنے کے لیے مشین کی مناسب دیکھ بھال، پہیے کا انتخاب، اور ورک پیس ہینڈلنگ کے امتزاج کی ضرورت ہوتی ہے۔ آپریٹرز کو فوری طور پر مسائل کی نشاندہی اور حل کرنے کے لیے باقاعدہ معائنہ اور دیکھ بھال کے طریقوں کو نافذ کرنا چاہیے، جس کے نتیجے میں پیسنے کی کارکردگی اور معیار میں بہتری آئے گی۔
پیسنے میں لوڈنگ کے مسائل
پیسنے میں لوڈنگ سے مراد وہ رجحان ہے جہاں پیسنے والے پہیے پر کھرچنے والے دانوں کے درمیان خالی جگہیں زمینی مواد سے بھر جاتی ہیں، جس کے نتیجے میں کاٹنے کی کارروائی کم ہوتی ہے اور رگڑ میں اضافہ ہوتا ہے۔ لوڈنگ پیسنے کے عمل کی کارکردگی اور معیار پر منفی اثر ڈال سکتی ہے۔ لوڈنگ کے مسائل کو حل کرنے کی ممکنہ وجوہات اور حل یہ ہیں:
نرم ورک پیس مواد:
وجہ:نرم مواد کو پیسنے سے کھرچنے والے دانے تیزی سے بند ہو سکتے ہیں۔
حل:نرم مواد پر کام کرتے وقت پیسنے والے پہیے کا استعمال کریں جس میں کھردری اور کھلی ساخت ہو۔ یہ فوری لوڈنگ کو روکنے میں مدد کرتا ہے اور چپ کو موثر طریقے سے ہٹانے کی اجازت دیتا ہے۔
مواد کی آلودگی:
وجہ:ورک پیس کے مواد میں موجود آلودگی، جیسے تیل، چکنائی، یا کولنٹ کی باقیات، لوڈنگ میں حصہ ڈال سکتے ہیں۔
حل:آلودگی کو دور کرنے کے لیے پیسنے سے پہلے ورک پیس کی مناسب صفائی کو یقینی بنائیں۔ لوڈنگ کو کم سے کم کرنے کے لیے مناسب کاٹنے والے سیال یا کولنٹس کا استعمال کریں۔
کولنٹ کی غلط درخواست:
وجہ:کولنٹ کا ناکافی یا غلط استعمال ناکافی پھسلن اور ٹھنڈک کا باعث بن سکتا ہے، جس کے نتیجے میں لوڈنگ ہوتی ہے۔
حل:کولنٹ کے بہاؤ اور ارتکاز کو بہتر بنائیں۔ اس بات کو یقینی بنائیں کہ کولنٹ مؤثر طریقے سے گرائنڈنگ زون تک پہنچ جائے تاکہ عمل کو چکنا اور ٹھنڈا کیا جا سکے، لوڈنگ کو روکا جائے۔
ناکافی وہیل نفاست:
وجہ:پھیکے یا پھٹے ہوئے پیسنے والے پہیے لوڈ ہونے کا زیادہ شکار ہوتے ہیں کیونکہ وہ اپنی کاٹنے کی صلاحیت کھو دیتے ہیں۔
حل:پیسنے والے پہیے کو باقاعدگی سے تیار کریں اور اس کی نفاست برقرار رکھنے کے لیے اسے تیز کریں۔ تازہ کھرچنے والے دانوں کو ظاہر کرنے اور کاٹنے کے عمل کو بڑھانے کے لیے وہیل ڈریسر کا استعمال کریں۔
کم پہیے کی رفتار:
وجہ:پیسنے والے پہیے کو کم رفتار سے چلانے سے چپس کو نکالنے کے لیے کافی سینٹری فیوگل قوت فراہم نہیں ہو سکتی، جس کی وجہ سے لوڈنگ ہوتی ہے۔
حل:یقینی بنائیں کہ پیسنے والی مشین مخصوص پہیے اور ورک پیس کے امتزاج کے لیے تجویز کردہ رفتار سے چلتی ہے۔ تیز رفتار چپ کو بہتر طریقے سے ہٹانے میں مدد کر سکتی ہے۔
ضرورت سے زیادہ دباؤ:
وجہ:پیسنے کے دوران بہت زیادہ دباؤ ڈالنے سے مواد کو وہیل میں زبردستی لگ سکتا ہے، جس سے لوڈنگ ہو سکتی ہے۔
حل:اعتدال پسند اور مسلسل پیسنے کا دباؤ استعمال کریں۔ فیڈ کی شرح کو ایڈجسٹ کریں تاکہ وہیل کو زیادہ دباؤ کے بغیر مؤثر طریقے سے کاٹنے کی اجازت دی جائے جو لوڈنگ کا باعث بنتا ہے۔
غلط پہیے کی وضاحتیں:
وجہ:مٹیریل گراؤنڈ ہونے کے لیے غلط تصریحات کے ساتھ پیسنے والے پہیے کا استعمال لوڈنگ کا باعث بن سکتا ہے۔
حل:مخصوص ایپلی کیشن کے لیے مناسب کھرچنے والی قسم، گرٹ سائز، اور بانڈ کے ساتھ پیسنے والا وہیل منتخب کریں۔ پہیے کو مواد سے ملانا لوڈنگ کو روکنے میں مدد کرتا ہے۔
کولنٹ کی ناکافی صفائی:
وجہ:آلودہ یا پرانا کولنٹ لوڈنگ کے مسائل میں حصہ ڈال سکتا ہے۔
حل:آلودگیوں کے جمع ہونے کو روکنے کے لیے باقاعدگی سے کولنٹ کو صاف اور تبدیل کریں۔ تازہ اور صاف کولنٹ پھسلن اور ٹھنڈک کو بڑھاتا ہے، لوڈنگ کے امکانات کو کم کرتا ہے۔
ڈریسنگ کی غلط تکنیک:
وجہ:پیسنے والے پہیے کی غلط ڈریسنگ بے قاعدگیوں اور لوڈنگ کا باعث بن سکتی ہے۔
حل:مناسب ڈریسنگ ٹول کا استعمال کرتے ہوئے پہیے کو مناسب طریقے سے تیار کریں۔ اس بات کو یقینی بنائیں کہ وہیل پروفائل مستقل ہے اور لوڈنگ کو روکنے کے لیے بے قاعدگیوں سے پاک ہے۔
لوڈنگ کے مسائل کو مؤثر طریقے سے حل کرنے میں وہیل کے مناسب انتخاب، مشین کے سیٹ اپ اور دیکھ بھال کے طریقوں کا مجموعہ شامل ہے۔ آپریٹرز کو تجویز کردہ طریقہ کار پر عمل کرنا چاہیے، مناسب پیسنے کے پیرامیٹرز کا استعمال کرنا چاہیے، اور لوڈنگ کو کم سے کم کرنے اور پیسنے کی کارکردگی کو بہتر بنانے کے لیے وہیل ڈریسنگ کو باقاعدہ نافذ کرنا چاہیے۔
مختلف دھاتی کام اور من گھڑت ایپلی کیشنز میں بہترین نتائج حاصل کرنے کے لیے صحیح پیسنے والی ڈسک کا انتخاب بہت ضروری ہے۔ انتخاب کا انحصار اس بات پر ہوتا ہے کہ جس مواد پر کام کیا جا رہا ہے، مطلوبہ تکمیل، اور استعمال ہونے والی چکی کی قسم۔
دائیں پیسنے والی ڈسک کا انتخاب
مواد کی مطابقت:
فیرس دھاتیں (اسٹیل، آئرن):خاص طور پر فیرس دھاتوں کے لیے تیار کردہ پیسنے والی ڈسک کا استعمال کریں۔ ان ڈسکس میں اکثر اسٹیل کی سختی کے لیے موزوں کھرچنے والی چیزیں ہوتی ہیں اور ان میں لوڈنگ کا خطرہ کم ہوتا ہے۔
الوہ دھاتیں (ایلومینیم، پیتل):رگڑنے سے بچنے کے لیے نرم دھاتوں کے لیے موزوں کھرچنے والی ڈسکس کا انتخاب کریں۔ ایلومینیم آکسائیڈ یا سلکان کاربائیڈ ڈسکس عام انتخاب ہیں۔
کھرچنے والا مواد:
ایلومینیم آکسائیڈ:فیرس دھاتوں پر عام مقصد کے پیسنے کے لئے موزوں ہے۔ یہ پائیدار اور ورسٹائل ہے۔
زرکونیا ایلومینا:اعلی کاٹنے کی کارکردگی اور لمبی عمر پیش کرتا ہے، اسے فیرس اور غیر الوہ دھاتوں پر جارحانہ پیسنے کے لیے موزوں بناتا ہے۔
سلکان کاربائیڈ:الوہ دھاتوں اور پتھر کو پیسنے کے لیے مثالی۔ یہ ایلومینیم آکسائیڈ سے تیز لیکن کم پائیدار ہے۔
گرٹ سائز:
موٹے گرٹ (24-36):تیزی سے اسٹاک کو ہٹانا اور ہیوی ڈیوٹی پیسنا۔
میڈیم گرٹ (40-60):اسٹاک ہٹانے اور سطح ختم کرنے میں توازن رکھتا ہے۔
فائن گرٹ (80-120):سطح کی تیاری اور ہلکی پیسنے کے لیے موزوں ایک ہموار تکمیل فراہم کرتا ہے۔
وہیل کی قسم:
قسم 27 (ڈپریسڈ سینٹر):ایک فلیٹ سطح کے ساتھ معیاری پیسنے والی ڈسک، سطح پیسنے اور کنارے کے کام کے لیے مثالی ہے۔
قسم 29 (مخروطی):جارحانہ اسٹاک کو ہٹانے اور سطح کی بہتر ملاوٹ کے لیے زاویہ دار ڈیزائن۔
قسم 1 (سیدھا):کٹ آف ایپلی کیشنز کے لیے استعمال کیا جاتا ہے۔ یہ درست کاٹنے کے لیے ایک پتلی پروفائل فراہم کرتا ہے۔
درخواست:
پیسنا:مواد کو ہٹانے اور تشکیل دینے کے لئے معیاری پیسنے والی ڈسکس۔
کاٹنا:دھات کو کاٹنے کے لیے کٹ آف پہیے کا استعمال کریں، ایک سیدھا اور صاف کنارہ فراہم کریں۔
فلیپ ڈسکس:ایک میں پیسنے اور ختم کرنے کو یکجا کریں۔ ملاوٹ اور سطحوں کو ہموار کرنے کے لیے موزوں ہے۔
گرائنڈر کے ساتھ مطابقت:
اس بات کو یقینی بنائیں کہ پیسنے والی ڈسک استعمال کی جا رہی گرائنڈر کی قسم اور رفتار سے مطابقت رکھتی ہے۔ ڈسک کے زیادہ سے زیادہ RPM (Revolutions per Minute) کے لیے مینوفیکچرر کی سفارشات کو چیک کریں۔
کام کی خصوصیت:
بھاری اسٹاک ہٹانا:موثر مواد کو ہٹانے کے لیے ایک موٹے گرٹ اور ٹائپ 27 یا ٹائپ 29 ڈسک کا انتخاب کریں۔
سطح کی تکمیل:ہموار تکمیل کے لیے فلیپ ڈسکس کے ساتھ درمیانے سے باریک گرٹس کا انتخاب کریں۔
حفاظت کے تحفظات:
حفاظتی ہدایات پر عمل کریں، بشمول مناسب ذاتی حفاظتی سامان (پی پی ای) جیسے حفاظتی شیشے اور دستانے پہننا۔
اضافی استحکام اور حفاظت کے لیے مضبوط ڈسکس کا انتخاب کریں۔
برانڈ اور معیار:
معیار اور مستقل مزاجی کے لیے معروف برانڈز سے ڈسکس منتخب کریں۔ اعلیٰ معیار کی ڈسکس بہتر کارکردگی اور استحکام پیش کرتی ہیں۔
لاگت پر غور:
پیسنے والی ڈسک کی متوقع عمر اور کارکردگی کے ساتھ ابتدائی لاگت کو متوازن رکھیں۔ اعلیٰ معیار کی ڈسکس کی ابتدائی قیمت زیادہ ہو سکتی ہے لیکن وقت کے ساتھ بہتر قیمت فراہم کر سکتی ہے۔
ان عوامل پر غور کرنے سے، آپریٹرز اپنی مخصوص ایپلی کیشنز کے لیے صحیح پیسنے والی ڈسک کا انتخاب کر سکتے ہیں، کارکردگی، حفاظت، اور بہترین نتائج کو یقینی بنا کر۔
نتیجہ
آخر میں، مناسب پیسنے والی ڈسک کا انتخاب میٹل ورکنگ اور فیبریکیشن کے کامیاب نتائج حاصل کرنے کا ایک اہم پہلو ہے۔ انتخاب کا انحصار مختلف عوامل پر ہوتا ہے جیسے کہ جس مواد پر کام کیا جا رہا ہے، مطلوبہ تکمیل، اور استعمال میں گرائنڈر کی قسم۔ مواد کی مطابقت، کھرچنے والی قسم، گرٹ سائز، پہیے کی قسم، ایپلی کیشن، گرائنڈر کی مطابقت، کام کی مخصوصیت، حفاظت، برانڈ کے معیار اور لاگت پر غور کرکے، آپریٹرز اپنے پیسنے کے عمل میں کارکردگی اور حفاظت کو بڑھانے کے لیے باخبر فیصلے کر سکتے ہیں۔
حفاظتی ہدایات پر عمل کرنا، مناسب ذاتی حفاظتی سامان پہننا، اور گرائنڈر اور ڈسک کی مطابقت کے لیے مینوفیکچررز کی سفارشات پر عمل کرنا ضروری ہے۔ چاہے یہ بھاری اسٹاک کو ہٹانے، سطح کو ختم کرنے، یا کاٹنے والی ایپلی کیشنز کے لیے ہو، دائیں پیسنے والی ڈسک کام کے معیار اور کارکردگی کو نمایاں طور پر متاثر کر سکتی ہے۔
مزید برآں، وقتاً فوقتاً ٹوٹ پھوٹ کی جانچ، زیادہ گرمی اور کمپن کے خدشات جیسے مسائل کو حل کرنا، اور لوڈنگ کے مسائل کو سمجھنا پیسنے والی ڈسک کی زندگی کو طول دینے اور مسلسل کارکردگی کو یقینی بنانے میں معاون ہے۔
خلاصہ یہ کہ، پیسنے والی ڈسکس کو منتخب کرنے، استعمال کرنے اور اسے برقرار رکھنے کے لیے ایک باخبر اور منظم طریقہ کار بہترین نتائج کے حصول، پیداواری صلاحیت کو بڑھانے، اور کام کرنے کے محفوظ ماحول کو یقینی بنانے کی کلید ہے۔
پوسٹ ٹائم: جنوری 12-2024